The Stocktake and Audit tool is designed to help with periodic reconciliations of your inventory, ensuring that the information held in your database is fully accurate and up to date.
When a stocktake is active, members of an inventory can move quickly location-to-location, using barcode scanners to check off containers which are present. We recommend stocktakes are conducted at least annually to ensure that your data remains accurate.
During a stocktake, there are three possible outcomes for each container record: when a container is scanned in the location where it is saved, it is marked off as being present; if a container is scanned in a different location than where it is saved, it is automatically moved into the correct location; and finally, any containers which were not scanned during the stocktake can be moved into a specified location (e.g. 'Missing').
Starting a Stocktake
Stocktakes can be started by users with Group Administrator privileges from the Barcodes/Labels menu on the Inventory Management page. Open the Stocktake & Audit information panel, then click on the Launch a Stocktake button.
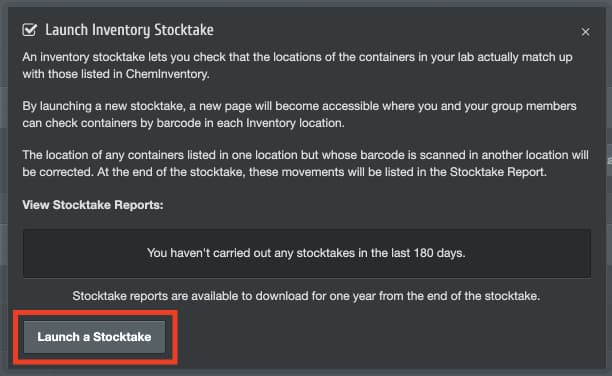
When a stocktake is active, all members of an inventory (except those with Read-Only privileges) have access to the Stocktake page which can be opened from the left navigation bar. The administrator who started the stocktake will be redirected automatically to this page when the stocktake is launched.
During a Stocktake
Before scanning containers, users must first open the Stocktake page then select the target location that is being checked. A summary of the container records saved in the selected location will be displayed on the right side of the page.
The containers listed will update over time as barcodes are scanned, with the container status shown by its border color: a green border indicates the container has been scanned in the correct location; a yellow border indicates that a container has been moved into the active location as a result of a scan; while a red border indicates that a container saved in the selected location has actually been scanned elsewhere.
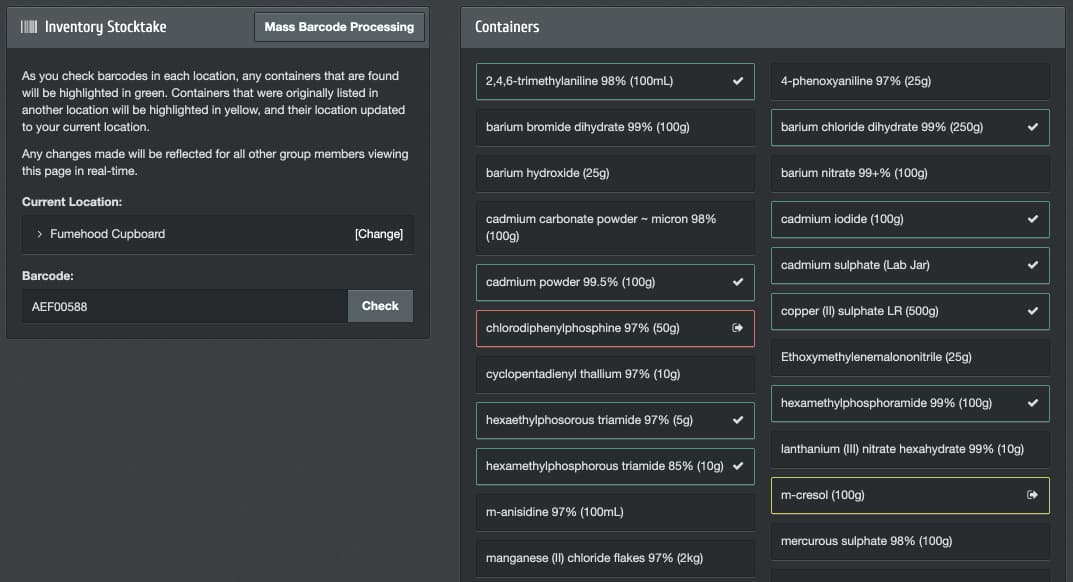
If you wish to process more than one barcode at a time, click on the Mass Barcode Processing button at the top of the page. This can be useful if you are using a wireless barcode scanner with on-board memory.
The Stocktake page can be used by any number of users concurrently, and opened on as many computers or devices as you need. Multiple users can be actively scanning in the same location at the same time.
Ending a Stocktake
When you have completed all locations, the active stocktake can be ended by a user with Group Administrator privileges from the Stocktake page, by clicking on the red End Stocktake button displayed at the top of the left column.
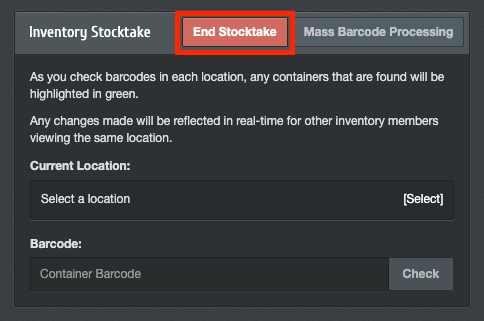
At this time ChemInventory will identify the containers (if any) which were not scanned during your stocktake. You will then be presented with the choice of either leaving these containers in the locations where they were saved previously, or moving them all to a selected location (e.g. 'Missing').
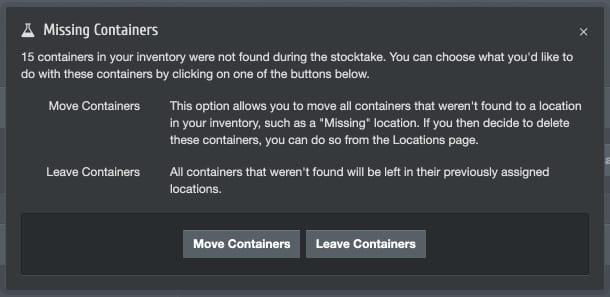
If you would like to delete the records of containers which were not found, select the Move Containers option and choose a destination location. You can then delete all container records in this location by heading to the Locations page, browsing to the selected location and then clicking on the Delete All button.
The Stocktake report
All activity that occurred during a stocktake will be summarized in a stocktake report which is generated when a stocktake is ended. Users with Group Administrator privileges can download this report from the Stocktake & Audit panel.